金属或陶瓷粉末注塑成型工艺
使用金属或陶瓷粉末通过注塑成型工艺生产复杂零件
如今,使用粉末材料的注塑成型技术主要用于制造工业用复杂组件。 粉末注塑成型是除了其它成型工艺(精密铸造和轴向或均衡压制)外的另一种可供选择的工艺。
近年来,用陶瓷或金属粉末来制造注塑成型零件的应用领域主要包括汽车工业、刀具工业、磁体生产、纺织工业、钟表工业、家居用品、精密工程、医疗和牙科技术以及陶瓷工业。
在 ARBURG PIM 实验室,客户可以通过实际观看样品生产来了解粉末注塑的优点。
表1: 金属和陶瓷组件的典型公差
粉末注塑成型技术使组件的批量生产成为可能,因为采用机械加工或压制技术进行批量生产已经不再是一种经济有效的方式。注塑成型技术使组件的设计和制造过程具有几乎无限的自由度。
粉末注塑成型制造过程包括成型零件的初始注塑成型、脱脂和烧结。 组件公差由以下重要因素确定:
● 粘合剂含量
● 粉末特性
● 混合过程
● 注塑成型参数
● 重力变形
● 在烧结托盘上的滑动性能
可用材料范围广泛
原则上,所有细颗粒、可烧结的粉末都可以和相应的粘合剂混合并在注塑机上加工。包括氧化陶瓷、金属、碳化物及氮化物。
由于混合和注塑设备在处理粉末材料的过程中会受到较强磨损,因此建议选择粒度尽可能小的粉末。 较细的粉末可降低表面粗糙度,从而在加工过程中降低磨损并提高生坯强度。 各种粉末材料的性能范围如表3中所示。
表2: 在严格的公差范围内的高重复性
粘合剂使粉末可用来注塑
对粘合剂最重要的要求是:脱脂过程中的尺寸稳定性、良好的保存特性、不与粉末材料发生反应、很高的零件强度、良好的脱模特性、热稳定性和在脱脂过程中易于去除并可完全去除。
粘合剂与粉末颗粒之间的粘附力还应尽可能高,以便在注塑过程中增高压力不会使两个组份分离,而导致填充的零件不均匀。 为了获得良好的注塑成型特性并以低收缩率获得均匀的烧结质量,建议采用球形粉末。
具有最佳配比的粘合剂与粉末
在混合过程中,粘合剂和粉末混合成一种匀质的混合物,即原料。 市场上有出售金属粉末和陶瓷粉末的原料供货商。 他们供应的材料品种繁多,并不断推出新品。
因此,MIM(金属注塑成型)或 CIM(陶瓷注塑成型)所需的原料都是现成的,可立即用于注塑,而不再需要内部制作。如果可用材料的性能不能充分满足所需的用途,专业化的材料供货商可以开发并生产客户需要的特定原料。
注塑成型过程中的加工步骤
用原料(粉末/粘合剂的混合物)制造成型零件的过程与塑料的注塑成型过程相似。
▲ 预塑
在塑化单元中,原料的粘合剂部分会在温度的作用下熔化。
▲ 注塑
塑料混合物在高压下被注塑到固定在锁模装置中的模具中。 模具保持闭合,同时成型零件硬化。
▲ 开模
在零件冷却后,喷嘴会通过注塑装置的移动从模具位置移开。 锁模装置打开,注塑成型机的顶针系统会自动顶出成型零件。
▲ 零件脱模
使用机械手系统从模具中脱出易碎的零件而不造成损坏。 在粉末材料的注塑成型时,推荐使用此工艺来保护绿件免受震动或冲击,从而避免损害成型零件的质量。
及时适量生产
材料和模具的更换可以在不到 20 分钟之内完成,这使它适用于精益生产(Just-In-Time Production)。 由于具有各种自动化选配件,因此可在无需操作者太多参与的情况下,对由金属或陶瓷粉末制造的组件实现批量生产。
注塑成型机的结构
传统螺杆式注塑成型机由锁模装置、注塑装置和控制系统构成。 由两个半面构成的模具固定在锁模装置中。 锁模装置本身具有静止模板(即所谓的固定模板)和可移动范本。 当锁模装置合闭以及模具随之合闭时,即可以注入材料。 当通过打开锁模装置而打开模具时,即可将成型零件脱出。
注塑装置的结构
注塑成型机上的注塑装置由螺杆(用于进料、压缩混合料并去除气泡)、加热系统(将混合料加热到一定温度)和喷嘴(经过压缩和加热的材料通过该喷嘴在压力下注塑到模具中)构成。 注塑成型机的所有移动和生产过程都可以通过屏幕控制功能加以协调控制。 调节参数一经确定,即可以保存到数据媒体上,从而确保了以前使用的生产周期的可重复性。 在生产过程中,可以自动识别并分离不合格零件和合格零件。
注塑模具
塑料注塑成型技术中常用的模具设备(如滑板、抽芯机构、脱螺纹装置和内部压力传感器)也可以用于粉末材料的注塑成型。 不过,由于粉末/粘合剂熔化材料具有研磨性,因此必须保护模具型腔和注塑装置以防止磨损(例如通过特殊硬化工艺或合金)。
从绿色的成型压块中去除粘合剂
在脱脂过程中,粘合剂会通过催化剂、熔解或热分解作用从绿件中去除。
脱脂过程可以借助于能够有效加速化学反应顺序的适宜炉温和氛围来进行。 粘合剂被去除后,成型零件会变成多孔易碎的模型,即所谓的“棕件“。 在此情况下,零件仅通过极少量的残留粘合剂和范德瓦尔斯力保持稳定。 根据所使用的粘合剂系统,必须按照适用要求对脱脂炉进行专门的调整。
脱脂炉必须具有非常好的气体循环特性。唯一的例外是需要在脱脂过程中埋置零件的粘合剂系统。 生成的废气必须通过适当的下游系统进行处理(例如通过二次燃烧或使用催化转化器)。
形成机械稳定的粘合效果
为了牢固地粘合棕色成型压块的颗粒,零件需要在更高的温度中进行烧结(最高达2000℃)。
根据熔炉环境条件、温度-时间曲线及压力分配情况,该工序类似挤压烧结部件时所使用的工艺。通过扩散和/或液态产生以及晶体生长而形成最终的成型件。
注塑成型的烧结零件最高可以达到 99.9%的理论材料密度。 在选择了适当粉末的情况下,零件可以各向同性地收缩,即在烧结过程中各个方向上的收缩量相等。 烧结零件的特点是具有均匀的特性。 在注塑成型过程中生成的缺陷无法通过烧结进行修复。
在烧结后的改良工序中,大多就只需配合修整或者刃口打磨。在金属或陶瓷注塑中,精细的粉末及合适的模具表面可以保证极高的表面质量。
为向感兴趣的人实际演示粉末材料加工及其所有重要工艺步骤,ARBURG 建立了自己的 PIM 实验室。
在此,从原料开发、准备和注塑成型直到成型零件的脱脂和烧结,所有步骤都可以在实验室条件下进行测试。
ARBURG 的资深专家可以向客户说明每个循环步骤细节,例如,粉末和粘合剂适宜的混合比例、“绿件”生产、后处理方法,以及机器和模具设计。
ARBURG PIM 实验室
PIM 实验室可以为客户开发并生产 1/2 升左右到 100 升粉末的原料混合物。 为了优化原料的进料特性,必要时还可以将原料处理成均质的粒状物料。
该实验室装备有各种必要设备,可以执行当前市场上的所有脱脂过程。 对于使用HNO3 和 N2 的催化脱脂,实验室具有容量为 60 升的炉。 热脱脂可以在 120 升炉内进行。 炉体使用特殊的循环气体系统;可以对所有零件进行均匀的脱脂。
在 Soxlet系统中,还可以使用各种溶剂(丙酮、乙醇等)对绿件进行脱脂。
一台直径为 145 mm、有效长度为220 mm 的管式炉可用于烧结。H2、Ar 或N2 以及这些气体的混合物可用作炉内气体。
氧化性材料可以在两端加热的箱式炉内在氧化性气体下烧结到 1700℃。 有效容积为 1.2 升。
总结
粉末注塑成型适合于复杂、高精度成型零件的大批量生产;对具有内螺纹、难于加工的底切和不规则表面的组件实现简单、自动化的生产,同时保证出色的表面质量。
粉末材料注塑成型的好处包括:
● 批量生产
● 使用传统工艺无法生产的零件可以一步完成生产
● 实现复杂的成型零件设计
● 可以快速调整生产
● 成型零件表面质量高
● 成型零件尺寸稳定性高
● 零件无需费时耗资的再加工
● 可以自动化生产
● 生产基本无浪费
17898826917
邮 箱:40045692@qq.com
Q Q:40045692
地 址:上海市奉贤区南桥镇国顺路936号5幢
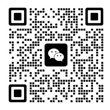
Copyright © 2018 上海道勤塑化有限公司 版权所有
备案号:沪ICP备19016906号