聚烯烃泡沫吹塑薄膜成型故障的排除
聚烯烃泡沫薄膜吹塑成型故障的排除故障名称成因及对策泡沫结构不规则(1)吹塑成型工艺条件控制不当。应适当调整。(2)熔体压力太低。排除方法为:①增加螺杆转速。由于发泡剂的分解与其在机筒内的滞留时间成正比,同时又受螺杆转速的支配,也就是说,适当提高螺杆转速,可使机头和口模内保持足够的压力,以抑制泡核增长,这是获得均匀、细密泡沫结构的必要条件。若转速太低,膜面会出现鲨皮斑。但螺杆转速也不能太高,否则会引起熔体破裂。②降低口模温度。为了使发泡在口模出口区开始,一方面要提高挤出压力,另一方面应维持稍低的口模和机头温度,以使模的出口压力等于或大于发泡的临界压力,防止提早发泡。③适当减小过滤板孑LB艮直径。④采用熔体流动速率较低的树脂。生产泡沫吹塑薄膜的常用树脂为低密度聚乙烯(LDPE)和低密度聚乙烯—醋酸乙烯共聚物,对于低密度聚乙烯,熔体流动速率以0.25—2.0g/min为宜,这种低熔体流动速率的树脂,具有较高的熔体强度和粘性。在熔体流动速率较低的低密度聚乙烯中加入5%—10%的醋酸乙烯,可增加薄膜的弹性及表面张力,改进泡沫薄膜的撕裂性能。⑤适当减小口模间隙。(3)口模挂料。排除方法为:①缩短口模定型段长度。定型段较长会发生气体扩散现象,因为熔料流过定型段时将产生压力降。②清除机头内的焦料杂质。(4)熔料在机头低压区滞流。排除方法为:①减小机头容量。设计机头时,应在保持流料均匀流动的前提下,尽量减小机头容量,以防止熔料在机头内滞留和释压。②增加螺杆转速。(5)在机头支架区成泡不规则。排除方法为:①采用螺旋式底部进料、缩短定型区或无定型区的小间隙机头。由于十字型机头支架周围容易产生压力变化,使气体从熔料中逸出,致使薄膜表面泡孔粗糙及不规则,故一般不予采用。②适当增加机头压力泡孔塌瘪(1)熔料流动不良。应改进机头流道结构及调整机头温度或挤出速度。(2)树脂熔体流动速率太高。应更换树脂。(3)泡管冷却太快。应降低冷却速度。值得引起重视的是,冷却是整个成型过程中较难控制的一个环节,它不仅直接关系到薄膜的生产速度,而且影响薄膜厚度的均匀性。通常采用减压室风环进行冷却,即在风环的出口设有空气转向板,使冷空气沿泡管表面平行流动,利用气流的减压度使泡管直径自动调节。由于骤冷和骤热会导致泡孔收缩和出现皱纹,所以,对泡管必须均匀而缓慢地冷却。(4)发泡剂与树脂混合不良。应改进混合条件。一般,将发泡剂加入树脂中有三种方法,即干粉混合法、液体分散法和母料法。分述如下:①干粉混合法。粉状发泡剂与颗粒树脂混合的方法最经济,但不易分散均匀,往往在熔料上结块,生成大泡孔,严重时使泡管缩小甚至塌瘪。对此,可在树脂表面喷涂一层矿物油,改善树脂与发泡剂的粘结性。②液体分散法。液态发泡剂可直接泵人挤出机,因此必须准确控制挤出速度和注入速度,以防止薄膜密度和泡孔结构发生变化。③母料法。母料法的生产成本较高,但它避免了干粉混合法的一系列缺陷。由于预制母料是一种发泡剂浓缩物,故能使发泡剂完全分解并有效地控制泡孔大小。再则,可保证每批原料具有恒定的发泡剂含量,因而适用于自动化加料膜面有针孔或破裂(1)发泡剂用量太多。应适当减少。(2)机头温度太高。应适当降低。(3)树脂熔体流动速率太高。应更换树脂或适当降低成型温度。(4)发泡剂分解太快。排除方法为:①适当增加螺杆转速。②适当减少发泡剂和活化剂的用量。活化剂的作用是加速发泡剂的分解和降低分解温度。供偶氮二甲酰胺(AC)发泡剂配用的活化剂有金属盐类,如氧化锌、硬脂酸锌等。一般认为,发泡剂的颗粒度愈小或表面积愈大,分解温度就愈低。但实践表明,不同粒度的发泡剂,在同样加热条件下,于同一温度范围放出的气体,仅在加入活化剂后才在一定范围内以不同速度进行分解,且分解速度可用发泡剂与活化剂的用量之比加以控制。一般两者比例为1:1时,效果较好薄膜表皮不良(1)发泡剂用量太多。应适当减少。常用的发泡剂为偶氮二甲酰胺(Ac),其用量一般根据薄膜的密度来确定,当加入0。5%(质量百分比)时,薄膜密度可下降30%—40%。(1)成型速度太低。应适当增加螺杆转速,提高挤出速度。(3)口模成型段熔体压力损失较大。排除方法为:①缩短口模定型段长度。②增大螺杆长径比。一般,螺杆的长径比以20:1或更大为宜。此外,对于聚烯烃来说,螺杆加料段长度应为直径的2倍,压缩段为直径的14倍,均化段为直径的4倍。螺杆的压缩比不能小于3。5:1。③适当增加螺杆转速。(4)机头温度太低。应适当提高
17898826917
邮 箱:40045692@qq.com
Q Q:40045692
地 址:上海市奉贤区南桥镇国顺路936号5幢
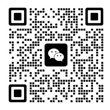
Copyright © 2018 上海道勤塑化有限公司 版权所有
备案号:沪ICP备19016906号