随形冷却对注塑成型和生产效率的影响
模具温度直接影响着注塑加工产品的质量和生产效率,它主要通过模具的冷却系统来进行适当的控制和调节。传统的冷却水道只能加工成简单的直孔,当注塑件形状复杂时#其冷却效果差,零件变形大。Jacobs发现使用铜镍合金材料制作的随形冷却注塑模具,其生产效率较传统冷却模具提高了70%左右,同时注塑制品的质量也有较大的改善。为此,本研究使用专业注塑过程模拟软件对注塑冷却过程进行三维冷却模拟,以研究随形冷却水道对注塑过程和生产效率的影响。
1 材料与方法
1.1 香盒零件的结构
以一个香盒零件为例,其结构如图1所示。零件外形尺寸为65mm×65mm×75mm。总体积为5.0×104mm3。该产品利用注塑成型,其材料为ABS,设定收缩率为0.55%。模具采用一模一腔结构,使用盘形浇注系统。
1.2 传统冷却方案
该香盒零件模具采用传统冷却水道(DCC)可设计三种冷却方案。方案一(DCC1)见图2(a)型腔采用单层冷却水道,直径为10mm;方案二(DCC2)见图2(b)型腔采用双层冷却水道,直径为10mm;方案三(DCC3)见图2(c)型腔采用三层冷却水道,直径为8mm另外,因型芯部分的最小直径只有35mm,故在三种冷却方案中均采用隔板式冷却水道,直径为18mm。
1.3 随形冷却方案
参考制品形状,模具型腔部位的冷却区域为圆柱面。对于随形冷却水道(CCC)可以设计两种冷却方案。方案一(CCC1)如图3(a)所示,采用螺旋形空间结构,冷却水道直径为8mm,方案二(CCC2)如图3(b)所示,采用圆环形空间结构,冷却水道直径为8mm。在两种随形冷却方案中,型芯部位仍然采取隔板式冷却。
1.4 注塑冷却有限元模拟
采用商用注塑模拟软件MPI进行注塑过程模拟。采用Fusion网格,其网格数为13270,配比率为92.1%,注塑材料选用Lustran ABS Elite HH1287。在MPI中建立的两种随形冷却方案的有限元模型如图4所示,其与模具冷却相关的工艺参数为:开模时间5s,保压时间10s填充时间1.7s,熔体温度230℃,模具温度50℃,冷却介质为水,温度为25℃,入口雷诺数为10000。
2 模拟结果与分析
使用MPI软件的C-W-F分析流程对香盒注塑制品进行注塑过程模拟,得出各冷却方案的成型周期C、冷却时间t和由冷却不均所引起的零件最大翘曲变形w如表1所示。
表1 几种冷却方案的模拟分析结果
从表1可以看出:对传统冷却方案,其冷却时间的大小排列为tDCC1>tDCC2>tDCC3,但在三套方案条件下冷却时间相差只有5%左右,由冷却不均匀引起的零件最大翘曲变形量w则刚好相反wDCC1<wDCC2<wDCC3。DCC1和DCC2相差只有3.7%明显增大,差距达到42.3%,从以上分析可以看出:使用传统冷却方法,随着冷却水道分布密度的增加其冷却效率略有增大,但由于其离型腔表面距离不相等,导致局部温度差增大,并最终增加了零件的翘曲变形。
相对于传统冷却方法!随形冷却方法的冷却时间缩短了40%,而由冷却不均匀引起的零件最大翘曲变形量也只有传统冷却方法的20%,此外,CCC2的成型周期和冷却不均匀引起的最大翘曲变形量均小于CCC1,即对该种零件结构,圆环形冷却结构要优于螺旋形冷却结构。
为了研究冷却过程中零件不同部位的冷却均匀性,分别选取传统和随形冷却方案中冷却效率最高、冷却水道分布密度相当的两种冷却方案(即DCC3和CCC2)做进一步对比分析。在香盒注塑模具的型腔表面从上到下均匀选取三个部位x,y,z,位置如图1所示。从模拟结果中采集温度数据,分析各个采样点从1.7-28.0s之间的型腔表面温度变化规律,两冷却方案中x,y,z三采样点的温度变化曲线如图5所示。
图5 三采样点的温度变化曲线
从图5中的温度变化曲线可以看出:在经过28.0s后,随形冷却水道模具的型腔表面温度为29℃,传统冷却水道模具为40℃,所以随形冷却水道的冷却速度明显优于传统冷却水道。另外,分析三采样点处的温度变化曲线可以发现:在随形冷却水道模具中,三点处的型腔表面温度差要小于传统冷却水道模具,表明随形冷却水道的冷却均匀性更优,这也是由随形冷却注塑模得到的注塑件翘曲变形量较小的原因。
3 随形冷却水道的实物验证
采用随形冷却方案CCC2,用选择性激光烧结(SLS)快速制模工艺完成模具的加工。其大致过程为:将模具模芯部分的三维STL模型导入SLS快速成形机中成型,之后进行脱脂、高温烧结、渗铜等后处理,处理完成后在模芯表面做简单机加工,再进行模芯与模架的装配,即完成了模具的制造过程。利用该模具进行注塑加工,得到香盒零件的注塑件如图6A所示。实际注塑过程中,冷却时间为18s左右,与模拟的误差只有10%最终注塑件变形小,无明显缺陷。
17898826917
邮 箱:40045692@qq.com
Q Q:40045692
地 址:上海市奉贤区南桥镇国顺路936号5幢
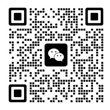
Copyright © 2018 上海道勤塑化有限公司 版权所有
备案号:沪ICP备19016906号