塑料中空容器成型技术的进步
随着中空吹塑成型技术(挤吹、注吹、注拉吹)的进步,特别是大型中空成型设备、多层共挤中空成型工艺及设备的发展,带动了其它中空成型技术的最新发展,它们包括气体辅助注塑件成型、半壳注射技术(shell technology)、旋转成型、吸塑成型技术等。 1、挤吹中空成型技术 挤吹中空塑料成型机是中空容器成型的主要设备,世界上80%~90%的中空容器是采用挤吹成型的。在我国中空塑料成型机的发展历程中,挤吹中空塑料成型机是发展最快和最完善的机种。近几年来,挤吹成型工艺技术的最新发展主要体现在三维(3D)吹塑复杂中空容器和大型包装容器上。 (1) 三维(3D)吹塑成型工艺 三维(3D)吹塑成型也称为少废料或者无飞边的吹塑成型。近年来,市场对复杂、曲折的输送管材制件的需求推动了这一技术的进步。3D吹塑成型工艺通常是使用6~8轴的机械手来运送型坯并将其放置在吹塑注塑件模具内进行吹胀。 (2) 大型中空吹塑成型技术 大型中空吹塑成型技术属于挤吹工艺。目前,采用大型吹塑机成型的容器主要是IBC桶(500~2000L)和200L双L全塑桶。 大型中空吹塑机一般包括挤出机、机头、合模装置、吹胀装置、型坯壁厚控制系统、制品取出装置、液压站和强弱电控制系统。一般的外辅设备包括混送料系统和余料粉碎回收系统等。按其挤出型坯的方式,大型中空机可分为储料式和连续挤出式,而按型坯的结构又可分为单层或多层。目前,国内的200L双L全塑桶绝大多数都采用单层储料式中空机吹制,下面就以该类大型吹塑机为例,从其最为重要的几个系统组成来介绍一下大型吹塑成型机的技术进展。 挤出机 大型中空机所加工的原料一般是HMWPE,所配置的挤出机若采用常规设计,则其塑化效率明显不足。例如,使用国产的f150/25挤出机来加工HMWPE粉料,其塑化能力仅为250kg/h。因此,大型中空机应采用带强迫喂料结构和强制冷却段结构的单螺杆挤出机,即具有IKV结构的挤出机。这种挤出机在相同长径比条件下,其塑化量较常规设计可提高50%以上,且挤出量稳定,再加之合理的屏障段和混炼段设计,还能获得很高的塑化质量。 储料式机头 储料式机头的流道主要有3种形式,即单层心形包络流道、双层心形包络流道和双层螺旋流道。 早期的中空机机头较多采用单层心形包络流道,这主要是因为当时对成型制品要求不高。而随着用户对容器质量要求不断提高,尤其在大型容器方面,存在熔合缝强度不足的问题,于是又出现了双层心形包络流道和螺旋流道的设计。双层心形包络流道之所以使融合缝区的强度得以提高,是因为可使挤出的型坯被完整的熔料层所覆盖,而不像单层心形包络流道那样会使型坯的圆周存在明显的熔合缝区。双层螺旋流道的优势则是内外层分别由两台挤出机供料,并同时储料。特别是由于制品的内层可以使用非着色料,使这种流道非常有竞争力。 对储料式中空机机头而言,衡量其水平的一个重要方面就是其换料的速度。尽管使用者希望换料的速度越快越好,但实际上却是很难实现的。即使是一个设计不错的机头,其换料时间也往往需要几个小时。虽然近几年出现了一种可提升流道的液压装置,通过它可实现外部清理,进而达到加速换料的目的,但该装置同时带来了机头结构庞大、制造和装配精度要求高以及实际清理时工人的劳动环境差等问题。因此,要想加快换料速度,首要任务是采用正确设计的流道,尽量减少滞留区域。 合模装置 近年来,大型中空机的合模装置逐步趋向于采用两板销锁式机构。该装置的移模运动是由油缸或伺服电机通过滚珠丝杠来实现的。由于采用了滚柱直线导轨,使其具有刚性高、运动精度高及运动轻快的优点。这种两板式合模装置的合模力是由两对或三对位置可调的销锁缸来实现的。为了方便注塑件模具安装,这些销锁缸可以简单地从模板上取下来,并通过沿轴向的调整来适应不同的注塑件模具厚度。与此相似的还有一种被称为“胡氏机构”的锁模装置,它的原理同销锁式机构基本相同,只是可以用在要求锁模力更大的合模机构上。在合模装置的液压控制方面,现在一般都采用比例液压阀,以精确控制合模的速度,进而有利于制品的成型。 型坯壁厚控制 中空吹塑机机头的型坯壁厚控制是中空成型的关键技术之一,其作用在全塑桶成型方面尤其显著。型坯壁厚控制分为轴向控制(AWDS)和径向控制(PWDS)两种形式。目前的大型中空机一般都具有轴向型坯壁厚控制功能,其控制点从24点到256点不等。轴向壁厚控制的作用是使得注出的料坯根据制品不同的吹胀比沿轴向获得不同的厚度,从而保证最终制品有比较均匀的壁厚分布。其原理是芯模根据预设位置作轴向运动,以改变模头的开口量,从而达到改变坯厚的目的。 2、多层共挤中空成型技术 基于多层吹塑中空容器在食品、化学品、化妆品、医疗卫生及其他工业包装方面的广泛应用,多层共挤中空成型技术得到了快速发展。 由于多层共挤中空成型机的复杂性,我国在这方面与先进国家相比还有较大的差距。虽然近几年国内也有一些机种推出,但还很不完善,需要从以下几个方面加强研究开发:研究适应一定范围的共挤机头(模头),以满足不同材料、不同层数及机头直径的要求;研究组合包装系统,它能根据不同的原料特制出可能允许的组合数的机头;研究基础机械程序。 3、气辅注塑件与水辅注塑件 气体辅助注塑件技术(GIT)通过把厚壁的内部掏空,能够成功地生产出厚壁、偏壁制品,在生产形状复杂的介质导管方面具有一定的优势。由于气辅技术可使制品的外观表面性质优异、内应力低、轻质高强,而且可节省材料、缩短生产周期,因此非常适合于家电、家具、汽车、办公用品、日用品以及玩具等领域的制品,其中包括管道状制件、大型扁平结构零件和由不同厚度截面组成的制件。 为了缩短冷却时间并获得较小的管子壁厚,用水代替气体来成型中空结构的注塑件技术被称为水辅注塑件(WAIM)。利用水辅注塑件的产品,壁厚更小,壁面更光滑。目前世界上有很多机构在进行与该项技术有关的研究开发。在水辅注塑件成型过程中,水像柱塞一样推动熔体迅速向前移动,在这个过程中,要求水不能蒸发,水前面的熔体也不能冻结固化,因而要求水的流量要达到20~80L/min,甚至更高。刚开始注水时,为了避免水的流速过高和压力过大(会在注水口附近产生漩涡而导致制品壁面缺陷),通常要对注水压力实行分级控制,即刚开始时压力较低,然后再把注水压力迅速提高到所需的水平。 4、半壳注塑件技术 半壳注塑件技术实际上是两种工艺过程的结合,即先用注塑件的方法生产两个半壳,然后再将两个半壳焊接起来而成为中空制品。为了保证这两种工艺流程能够很好的匹配,要求注塑件的两个半壳的焊接面必须非常平整,毫无翘曲。一般要利用计算机辅助工程(CAE)设计软件进行优化设计,以尽量消除因制件冷却不均匀而产生的内应力。 目前,使用半壳注塑件技术生产的中空产品有汽车仪表板上的各种气管、发动机进气管和汽车油箱等。 5、注塑件模具滑动注塑件成型 注塑件模具滑动注塑件成型法是由日本制钢所开发的一种用于制造中空制品的两步注塑件成型法。其原理是:首先将中空制品一分为二,对两部分分别注射而形成半成品,然后将两个半成品和注塑件模具滑动至对合位置。二次合模后,在制品两部分结合缝处注入塑料熔体(第2次注射),最后得到完整的中空制品。与吹塑制品相比,该技术所成型的产品具有表面质量好、尺寸精度高、壁厚均匀且设计自由度大等优点。 在制造形状复杂的中空制品时,注塑件模具滑动注塑件成型法与超声波焊接相比的优点是:不需要将半成品从注塑件模具中取出,因而可以避免半成品在注塑件模具外因冷却而造成制品形状和精度的下降,此外还可以避免焊接工艺中因产生局部应力而引起的熔接强度的降低。 6、旋转模塑 旋转模塑是指注塑件模具在加热的炉子内沿2个轴旋转,装在注塑件模具内的塑料熔结在注塑件模具表面,冷却后即可以得到与注塑件模具形状相仿的中空制品的技术。旋转模塑的优点是成型过程没有压力,从而使制品没有内应力,壁厚比较均匀(与吹塑和热成型相比),同时,注塑件模具也比较简单。该技术特别适合于小批量生产大型中空制品。 最初用于旋转模塑的主要材料是PVC糊塑料,目前则更多地使用聚乙烯、聚丙烯和尼龙。常见的旋转模塑产品有玩具、功能性家具、容器和储槽(最大容积可达80m3)、汽车零部件、体育休闲用品、交通隔离标志等。近几年,旋转模塑产品的增长速度较快,平均年增长率为20%,远远高于其他塑料制品的增长率。 旋转模塑可适用的塑料品种很少,因为该技术要求塑料具有较好的热稳定性,同时,由于需要将塑料磨成粉,使材料价格有所提高。此外,很难用成型加强肋的方法提高产品的刚度。 7、热成型工艺技术 热成型是对挤出热塑性片材通过一系列的成型或拉伸而得到制品的方法。具体来说就是通过加热使片材软化,然后借助真空或低压使软化的片材压向整个模面,从而得到既简单又经济的制品。这种成型的优点是注塑件模具费用低、注塑件模具研制周期短、注塑件加工房投资费用低、设备投资小且短时间里就可运转。 普通热成型 热成型需要较多设备,包括烘箱、注塑件模具及串联的辅助设备。真空辅助包模成型设备是其中最简单的一种。在单级设备里,切好的片材被夹在一个框架上,通过幅射(红外)加热使其软化。压紧在框架中的热片材被向下拉(预拉伸)到冷凸模上,上面受大气压,下面抽真空,软化的片材受到强压后就会紧贴冷凸模而成型。这种单级设备还可以进行带额外压力的热成型,即使加热的空气穿过多孔板吹向片材,将片材压向凹模里,片材受真空拉伸并紧贴向模壁,在此过程中空气压力可以高达1Mpa。在两级设备里,加热装置在成型区的外面,热片材夹在框架上进行来回输送。在普通热成型中,凸模通常比凹模有较大的拉伸度,但脱模较难,因而制件的外表面清晰度较差,而制件紧贴注塑件模具的内表面清晰度则相对较大。 双片热成型 双片热成型的特点是成型快、壁厚均匀,可以制作双色和厚度不同的制品,甚至材料不同的制品。在工艺上可分为双片压力热成型和双片真空热成型两种。其中,双片真空热成型的工艺是:先分别在注塑件模具内真空成型出2个片材,再将2个注塑件模具合模,施压使制品熔合成为中空制品,如有必要,甚至可以在空腔内放入其他构件。采用该方法成型的典型产品有冲浪板、油箱、小船、门、管道、玩具等。与吹塑工艺相比,用这种方法生产小型或中型产品时,效率更高。而与旋转模塑相比,这种方法不仅生产效率更高,而且可以适用更多的塑料片材,包括多层共挤出片材。
17898826917
邮 箱:40045692@qq.com
Q Q:40045692
地 址:上海市奉贤区南桥镇国顺路936号5幢
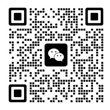
Copyright © 2018 上海道勤塑化有限公司 版权所有
备案号:沪ICP备19016906号